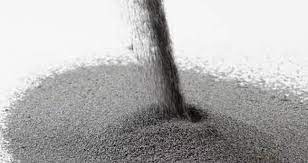
چگونگی تولید پودر فلزات(بخش چهارم): بررسی اتمیزاسیون گریز از مرکز و سایر روش های اتمیزاسیون در تولید پودر
ترجمه و تنظیم: دکتر فرشید ریخته گر
چکیده
در بخش های قبلی، در مورد دو روش متداول اتمیزاسیون با برخورد دو سیال که یکی (مذاب فلز)به صورت توده با دیگری (آب یا گاز) برخورد نموده و به ذرات ریزی شکسته میشود، نکاتی بحث و مطرح گردید. در این بخش روش های دیگری از اتمیزاسیون، شامل تجزیه مکانیکی جت مذاب و تبدیل آن به قطرات فلز ارائه می شود. برخی از این فرآیندها مانند اتمیزاسیون گریز از مرکز به طور مناسبی تثبیت شده و با ظرفیت حدود ۱۰۰ – ۵۰ کیلو تن در سال در مقیاس صنعتی به بهره برداری رسیده اند. روش اتمیزاسیون التراسونیک، چندین دهه به صورت تجاری برای آلیاژهای دمای پایین به کار گرفته شده است و پیشرفت های اخیر باعث شده تا دمای کاری آن افزایش یافته و قابلیت فرآوری طیف وسیعی از آلیاژها را داشته باشد. همچنین در این بخش، نگاهی به اتمیزاسیون فشاری (یا تک سیاله) خواهیم داشت که کاربرد بسیار محدودی دارد و نیز به طور اختصار، برخی فرآیندهای دو سیاله با استفاده از سیال های نامتعارف(مانند روغن و گاز برودتی) تشریح خواهد شد.
اتمیزاسیون گریز از مرکز
در برخی موارد به این روش، اتمیزاسیون چرخشی نیز گفته می شود و در اصل به مفهوم شکست جت مذاب به وسیله نیروهای گریز از مرکز است. یک تصویر کلی و روشن از این ویژگی در شکل ۱ نشان داده شده است. در این شکل یک جت مذاب از جنس فولاد با سرعت t/h 30 روی یک دیسک یا کاپ با قطر mm 600 سقوط می کند. در اثر چرخش با سرعت کم، ذرات نهایی بسیار درشت می گردد. مکانیزم فرآیند بدین صورت است که مذاب تا رسیدن به سرعت جانبی دیسک شتاب می گیرد و سپس قطرات یا لیگامنت ها شکل می گیرند و در ادامه، این لیگامنت ها مجدد ا به قطرات ریزتر تبدیل می شوند. اگر سیلان فلز به میزان کافی بزرگ بوده و دیسک به اندازه لازم کوچک باشد، در برخی موارد مذاب به شکل ورقه هایی در آمده و سطح دیسک را ترک می نماید. در برخی حالت ها، مدل سازی فرآیند اتمیزه چرخشی نسبتا آسان است. تعادل بین نیروهای گریز از مرکز و کشش سطحی از طریق رابطه زیر بیان می گردد:
رابطه (۱)
۰.۵ D= k/ω×(γ/ρd)
که در آن:
d : قطر دیسک یا کاپ
ω : سرعت زاویه ای دیسک یا کاپ
ρ : چگالی مذاب
γ : کشش سطحی مذاب
D : اندازه ذرات پودر می باشد.
بنابراین بر اساس رابطه فوق می توان نتیجه گرفت که اندازه ذرات، به طور معکوس با سرعت چرخش دیسک، به طور مستقیم با مجذور کشش سطحی مذاب و به طور معکوس با مجذور چگالی مذاب و قطر کاپ ارتباط دارد. رابطه فوق میتواند برای آزمودن امکان سنجی عملی در ساخت اندازه ذرات پودر مورد نیاز به این روش به کار برده شود. واضح است که کشش سطحی بالا و چگالی کم (مانند فلزات Al ، Mg ، Ti) پودر های درشت تری تولید نموده و در عوض، کشش سطحی کم و چگالی زیاد(مانند Pb و Sn ) منجر به تولید ذرات پودر ریزتری می گردد.
در به کارگیری اتمایزر گریز از مرکز، توجه به دو نکته زیر قابل تامل است:
۱ – خواص ماده انتخابی برای کاپ یا دیسک(محدودیت های نسبت دما/ استحکام و واکنش پذیری)
۲ – فاصله پرواز برای قطرات تا زمان انجماد آنها
به طور مشخص، اگر ماده مورد نیاز برای تهیه پودر، مانند Ti دارای نقطه ذوب بالا و واکنش پذیری زیاد باشد، طراحی و انتخاب ماده برای دیسک، بسیار چالش برانگیز خواهد بود. همچنین، اگر ذرات پودر بسیار درشت مدنظر باشد، نیاز به فاصله پرواز بسیار زیادی بوده تا انجماد قطرات کامل شود، به گونهای که بر اساس آن قطر محفظه اتمایزینگ تا بیش از m 10 افزایش می یابد.
شکل ۱ : اتمیزاسیون گریز از مرکز در یک کاپ در حال چرخش
برخی واحدهای تولید با این شرایط و با دستگاه بزرگ کار می کنند، اما توجیه آن بر اساس حجم بالای پودر مورد نیاز و پیوستگی فرآیند ساخت برقرار می شود. سیستم های با این ابعاد، معمولا برای تمیزکاری در زمان تغییر فلز/ آلیاژ دچار چالش می شوند، لذا اغلب از آن ها به طور اختصاصی برای تولید یک نوع پودر استفاده می گردد. یکی از مزایای مهم این روش، قابلیت دستیابی به توزیع اندازه ذرات بسیار باریک است. انحراف استاندارد توزیع لگاریتمی ذرات( ۵۰/d84d ) در این روش بسیار کمتر از فرآیندهای دو سیاله می باشد که در آنها رسیدن به مقادیر انحراف کمتر از ۲ بسیار دشوار است (شکل ۲)
در بهترین حالت این نسبت در اتمیزاسیون گریز از مرکز بین ۴ / ۱ – ۳ / ۱ قرار می گیرد. این بدان معناست که راندمان تولید پودر در یک محدوده باریک (مانند اندازه پودر بین μm 100 – 50 ) که در اتمیزه دو سیاله از ۴۰ % فراتر نمی رود، با این روش به بیش از ۶۷ % می رسد و میزان پودر باقیمانده با ابعاد ۴۰+μm -۱۴۰ از میزان ۵۸ % به ۹۰ % افزایش پیدا می کند. با در نظرگیری اصول فرآیند شامل حرکت ذرات با فاصله از یکدیگر، تشکیل پیرا ذرات به ندرت رخ داده و انجام عملیات تحت اتمسفر خنثی، منجر به تولید ذرات مناسب از لحاظ کرویت می گردد. مزیت دیگر این فرآیند نسبت به روشهای دو سیاله آن است که انرژی لازم برای چرخش کاپ در حالت حداقل قرار دارد. این موضوع در حالتی اهمیت می یابد که نیروی محرکه لازم برای یک کمپرسور در روش اتمیزاسیون گازی، مقدار قابل توجهی انرژی مصرف می کند. اما در این روش، حتی در حالتی که نیاز به تزریق گاز خنثی وجود دارد، مصرف ویژه گاز بسیار پایین بوده و از لحاظ اقتصادی مقرون به صرفه می باشد. زمینه اصلی کاربرد اتمیزاسیون گریز از مرکز در تولید پودر مورد نیاز لحیم کاری سرد با گرید تجهیزات الکترونیک است. ویژگی های این محصول شامل کرویت عالی و میزان اکسیژن کم ( ۱۰۰ppm >) و محدوده باریک اندازه ذرات برای آلیاژ لحیم نوع ۴ ( ۲۰+/۳۸-µm) است.
به علاوه، این آلیاژها دارای نقطه ذوب کم و چگالی بالا بوده و کشش سطحی کمی دارند و به این ترتیب امکان تولید پودرهای ریز از آنها وجود دارد.
برای ساخت دیسک اغلب از فولادهای ساده کربنی استفاده می شود تا بتوانند در برابر حرارت و سایش آلیاژ مقاومت نمایند. شکل ۳ یک سیستم اتمیزاسیون گریز از مرکز با قطر محفظه m 2/5 ، قطر دیسک mm 30 ، با قابلیت چرخش rpm 60000 و ظرفیت تولید Kg/h 200 پودر لحیم SAC (Sn-Ag-Cu) را نشان می دهد. به طور کلی، مواد مورد نیاز برای ساخت دیسک قابل تهیه هستند، اما در مواردی، برخی از شاخص های ویژه آنها به
آسانی یافت نمی شوند.
پودر روی هم به عنوان یک فلز متداول با استفاده از اتمیزه گریز از مرکز به میزان قابل توجهی تولید می شود و در ساخت باتری های آلکالین به کار می رود. در اینجا نیز توزیع اندازه ذرات باید بسیار باریک باشد و ابعاد ذرات تا حد امکان درشت در نظر گرفته شود. در حال حاضر، تولید پودر روی با ظرفیت بیشتر از ۱t/h قابل دستیابی بوده، اما جهت ساخت ذرات درشت تر نیاز به محفظه بزرگ با قطر m 10 وجود دارد. استفاده از فرآیند ذوب پیوسته امری رایج بوده و انتقال پیوسته پودر تولیدی به بخش تفکیک و غربال به صورت نرمال انجام می پذیرد.
شکل :۲ منحنی های لگاریتم طبیعی توزیع اندازه ذرات برای پودرهای اتمیزه؛ شماره های ۳ و ۷ مربوط به محصوالت گریز از مرکز و سایر منحنی ها شامل محصوالت فرآیندهای اتمیزه آبی یا گازی
آلومینیم هم به عنوان یک فلز مناسب برای اتمایزینگ مطرح است، اما با توجه به چگالی کم و کشش سطحی زیاد آن، ملاحظات فیزیکی بیشتری روی چرخش کاپ اعمال می شود و اغلب برای تولید پودر های ریزتر، سرعت های چرخش بسیار بالایی مورد نیاز می باشد. بنابراین، به کارگیری روش گریز از مرکز معمولا برای تولید پودر آلومینیم درشت تر در محدوده μm 100 – 700 انجام می پذیرد. منیزیم چالش های تولید در کاپ های فلزی به مانند آلومینیم را ندارد، اما از لحاظ ایمنی خطرات خاص خود را در تولید پودر دارد. اخیرا یک واحد سازنده پودر موفق به ساخت محصولی با اندازه میانگین μm 100 و با نرخ
تولید Kg/h 200 گردیده است.
شکل ۳ : (چپ) اتمایزر گریز از مرکز برای ساخت پودر لحیم کاری و (راست)نمایی از دیسک در حال چرخش
استفاده از روش اتمایزینگ گریز از مرکز برای آلیاژهای آهنی، به مقدار زیادی بستگی به جنس کاپ مورد استفاده دارد. فرآیند نرخ انجماد سریع ۱ ( RSR )، توسعه یافته توسط شرکتPratt & Whitney ، از یک دیسک مسی آبگرد در دستگاه خود استفاده می نماید و با استفاده از آن مواد بسیار فعال مانند سوپر آلیاژها، تیتانیوم، FeNdB و فولاد ها را فرآوری می نماید. نکته قابل توجه در این روش خنک شدن اسپری مذاب با گاز هلیوم است که هزینه بالایی را به بهره بردار تحمیل می نماید در حالیکه، خنک کاری سریع دلیل اصلی استفاده از گاز هلیوم نیست. ضمن اینکه کل سیستم قابلیت ایجاد خلأ برای فرآوری سوپر آلیاژها را دارد که موجب افزایش هزینه جداگانه خواهد بود. جزئیاتی از چیدمان این ماشین مطابق شکل ۴ منتشر شده است و به نظر می رسد در آینده بخش مهمی از این موارد دستخوش تغییرات خواهد شد.
پس از معرفی فرآیند RSR ، صنایع Ervin توانسته است تا اصلاحات و ارتقای لازم را برای این تکنولوژی از مقیاس آزمایشگاهی به تولید صنعتی انجام دهد و پودر مورد نیاز فرآیند MIM را با استفاده از آن تولید کند. در حال حاضر این شرکت قابلیت تولید انواع پودر از آلیاژهای متنوع را با شکل کروی کامل و پیراذرات کم در محدوده μm 1- 1000 با این روش پیدا نموده است. اتمایزر گریز از مرکز استاندارد دارای قطر محفظه بسیار بزرگی است و پودر به طور مناسب در آن خنک کاری نمی شود. برای رفع این موانع چیدمانی از کوئنچ تجهیزات با آب اضافه شده تا با بهره گیری از آن امکان تولید پودر آهنی از یک کوره با ظرفیت۱/ ۱ تن فراهم گردد (شکل ۵ ). این اقدام باعث افزایش راندمان به بیش از ۹۹ % در تولید ذرات پودر با اندازه مورد نیاز می شود. علاوه بر فلزات، این روش
برای فرآوری سرباره ها، نمک های مذاب و برخی شیشه های با ویسکوزیته کم نیز قابل استفاده است.
شکل ۴ : تصویر شماتیک از فرآیندRSR
شکل ۵ : چپ کوره ذوب ۲ / ۱ تن در حال تخلیه به اتمایزر با سیستم کوئنچ آب و
راست کاپ حین کار با ظرفیت تولید پودر ۵۰Kg/min
علاوه بر اتمایزرهای با تغذیه مذاب که تاکنون بحث شد، روش های نوینی مانند فرآیند الکترود چرخان ۱ ( REP ) یا الکترود چرخان با پلاسما ۲ ( PREP ) نیز توسعه یافته اند (شکل ۶). در اینجا یک میله چرخان با سرعت بالا ( rpm 10000 یا بیشتر) به عنوان لقمه اولیه عمل نموده و نوک آن ذوب می شود. در روش REP ، ذوب از طریق ضربه مستقیم قوس به میله و در روش PREP ، ذوب با استفاده از قوس پلاسمای انتقال یافته از مشعل تشکیل می شود. مورد دوم از تشکیل آخال های تنگستن (به ویژه در فرآوری تیتانیم) که به واسطه سایش معکوس الکترود ایجاد می گردند، جلوگیری به عمل می آورد. اگر چه در هر دو روش از میله چرخان به عنوان آند استفاده شده و باعث ایجاد توان الکتریکی بالایی در قطعه کار در حال گردش می شود و چالش هایی را ایجاد می کند. به همین منظور کارهایی در مورد استفاده از لیزر به عنوان منبع حرارتی ایجاد ذوب انجام شده که مشکلات انتقال توان الکتریکی به قطعه کار را مرتفع می سازد.
در مقایسه با دیگر روش های گریز از مرکز، توزیع اندازه ذرات در این روش ها بسیار باریک است در حالیکه، نرخ تولید در آنها متوسط بوده و در مقیاس چند ده کیلوگرم در ساعت قرار دارد. هزینه های بالا در ساخت میله های اولیه صاف و دقیق و همچنین نیاز به استفاده از نگهدارنده در انتهای میله، این روش ها را تا حدودی گران قیمت می کند. پیشرفت های اخیر در کشور چین نشان می دهد که امکان تولید پودرهای ریزتر با این روش نسبت به موارد مطرح شده قبلی (با میانگین اندازه تقریبا μm 100 ) وجود دارد که این کار از طریق افزایش سرعت چرخش قطعه کار انجام پذیر است.
شکل ۶ : چپ روش REP و راست پودر فولاد زنگ نزن تولید شده به روشPREP
اتمیزاسیون التراسونیک
به خوبی مشخص شده است که ارتعاشات التراسونیک میتواند پاششی از قطرات مذاب را ایجاد نماید. در صورتی که این کار روی فلز مذاب صورت گیرد، پودر فلز قابل تولید است. با این وجود، چالش های مواد انتخابی از نظر میزان ترشوندگی سطح قابل تامل بوده و تا حدودی به کارگیری این روش را محدود به آلیاژهای لحیم سرد با نقطه ذوب کم نموده است. فرآیند اتمیزاسیون التراسونیک دارای مزیت های مهم ذیل است:
- قطرات اتمیزه شده بسیار آهسته حرکت می کنند و در نتیجه، نیازی به استفاده از محفظه بزرگ نمی باشد.
- توزیع اندازه ذرات به مانند اتمیزاسیون گریز از مرکز بسیار باریک و مناسب است.
- مصرف انرژی و گاز در طول فرآیند به اندازه متوسط است.
با این وجود محدودیت هایی هم در این روش وجود دارد:
- نرخ تولید بسیار پایین (در حدود Kg/h 50 – 30) برای آلیاژهای لحیم سرد است.
- با افزایش فرکانس به منظور ایجاد توزیع ذرات ریزتر، نرخ تولید باز هم افت می نماید.
- با قرار دادن اتمایزر روی یک فرکانس ثابت، بسته به نوع آلیاژ فقط امکان تولید یک توزیع مشخص از ذرات وجود دارد. ضمن اینکه محدوده فرکانس های قابل دسترس نیز چندان گسترده نیست.
- برخی از آلیاژ های لحیم سرد منجر به سایش سطح لرزاننده می شوند.
به طور کلی این روش شامل ایجاد یک فیلم از مذاب بوده که قادر است سطح را تر نماید و در ادامه، این سطح تحت عملیات لرزش قرار می گیرد. امواج ایجاد شده، بسته به فرکانس ارتعاش و خواص مذاب، دارای یک طول موج مشخص هستند (شکل های ۷ و ۸).
شکل ۷ : چپ امواج ایستاده روی سطح در حال لرزش و راست شکل گیری قطره از موج ایستاده سطحی
شکل ۸ : اتمیزاسیون التراسونیک یک آلیاژ لحیم در فرکانس khz 40 ، مذاب از بالا آزاد شده و به سطح لرزش
(با حرکت توده امواج از پایین به بالا) برخورد می نماید.
کاربردهای اولیه اتمیزاسیون التراسونیک از نظر محدودیت دمایی و واکنش پذیری با مذاب، به جنس صفحه لرزش و دمای کوری ترانسفورماتور التراسونیک (برای صفحات غیر خنک شونده) وابسته بوده و بر همین مبنا، استفاده از این فرآیند به آلیاژهای لحیم با نقطه ذوب پایین تقلیل می یافت. پیشرفت های اخیر با بهره گیری از سیستم خنک کاری با آب برای صفحه لرزش، قابلیت دمایی آن را افزایش داده است. در یک حالت، سیستم شبیه به یک ذوب کننده متداول با قوس انتهایی است که در آن صفحه داغ با امواج التراسونیک ارتعاش می یابد. به علاوه، مطابق شکل ۹ تغذیه سیم به طور پیوسته، تامین مواد اولیه موردنیاز سیستم را انجام می دهد. اگرچه استفاده از سیم به عنوان لقمه اولیه فرآیند، توسعه آلیاژهای مورد استفاده را محدود می سازد زیرا، تولید سیم روشی هزینهبر بوده و برای تمام آلیاژها مقدور نیست.
در حالت دیگر، ذوب متداول القایی با بوته کف ریز جهت تامین جت مذاب استفاده شده و سپس مذاب به سمت صفحه لرزشی هدایت می گردد(شکل ۱۰ ). نرخ اتمیزاسیون با این روش تا بیش از Kg/h 3 گزارش شده است. اگرچه بهره گیری از این روش محدوده آلیاژهای قابل فرآوری را وسعت می بخشد، اما ریختن پیوسته و پایدار مذاب در نرخ سیلان کم امری دشوار است. در هر دو صورت فوق، امکان افزایش نرخ تولید تا اعداد مربوط به روش های متداول اتمیزاسیون وجود ندارد و بنابراین، این سیستم ها عموما جهت کاربردهای خاص معرفی می گردند و با وجود پیشرفت های اخیر، همچنان تولید پودر با روش التراسونیک در مقیاس کم و مطابق با نیاز و خواسته مشتری دارای توجیه اقتصادی است.
شکل ۹ : اتمایزر التراسونیک با تغذیه لقمه اولیه به شکل سیم
شکل ۱۰ : چپ( اتمایزر التراسونیک با سیستم بوته کف ریز در کوره القایی و راست) اتمایزر حین تولید پودر فلز
روش های دو سیاله ( ۱ ): اتمیزاسیون با روغن/ هیدروکربن
یکی از چالش های اتمیزه آبی، اکسیداسیون پودر فلزات است. استفاده از یک هیدروکربن غیر فرار، ترجیحا با نقطه اشتعال بالا به جای آب با تجهیزات تقریبا مشابه، امکان کاهش یا حذف کامل اکسیداسیون را فراهم می سازد. اگرچه، تفاوت های مهم ذیل می بایست مدنظر قرار گیرد:
۱ – حرارت ویژه کمتر هیدروکربن ها نسبت به آب، به مفهوم نسبت های بیشتر سیال/ فلز مورد نیاز به منظور
جلوگیری از ایجاد دمای بالای مخلوط سیال و پودر خواهد بود.
۲ – تزریق گاز نیتروژن به منظور جلوگیری از ایجاد احتراق توسط مذاب اجتناب ناپذیر می باشد.
۳ – بازیابی حلال در حین خشک کردن به دلایل اقتصادی و محیط زیستی ضروری است.
۴ – به واسطه تولید مقداری هیدروژن، هیدروکربن باید به متان یا اتان شکسته شده و یا با عملیات پیرولیز به کربن
و سایر مشتقات تبدیل گردد.
۵ – ملاحظات ایمنی ویژهای باید در نظر گرفته شود تا سایت تولید از هرگونه آتش سوزی در امان باشد.
پودر حاصل شده به این روش از لحاظ ابعاد مشابه با محصول اتمیزه آبی در فشار یکسان است، اما تفاوت هایی از چند منظر ذیل در اتمیزه با هیدروکربن وجود دارد:
میزان اکسیژن کم یا بدون اکسیداسیون سطحی
بی نظمی در پودر کمتر و تمایل بیشتر به حالت کروی
وجود ریسک هایی از نظر جذب کربن توسط پودر
در شکل ۱۱ مقایسه ای بین دو روش فوق از نظر چگالی ظاهری پودر محصول برای چند آلیاژ مختلف و در جدول ۱ مقایسه محصولات آلیاژی از نظر میزان عناصر کربن و اکسیژن موجود در پودر ملاحظه می گردد.
شکل ۱۱ : مقایسه چگالی ظاهری پودرهای اتمیزه شده با آب و روغن
جدول ۱ : میزان اکسیژن و کربن موجود در پودرهای اتمیزه شده با آب و روغن
به طور مشخص، فلزات آلومینیم و روی با فیلم های اکسیدی بسیار پایدار، افزایش قابل توجهی در چگالی ظاهری را به واسطه اتمیزه با روغن نشان می دهند که رابطه مستقیمی با تشکیل ذرات کروی به میزان بیشتر دارد. در مورد برنز Cu10Sn که واکنش کمی با آب دارد، اثر روغن کمتر محسوس است و این اثر برای آلیاژ Ni20Cr بسیار قابل توجه می باشد. در آلیاژ NiCrBSi که در حین ذوب در دمای سالیدوس تشکیل لایه اکسید بروسیلیکات می دهد، تاثیر کمی از تغییر سیال مشاهده می شود. با در نظرگیری جدول ۱ ، میزان اکسیژن پودر Al اتمیزه شده با آب در ماکزیمم مقدار قرار دارد در حالیکه، با روغن این میزان به حدود چند ppm می رسد. آلیاژهای با نقطه ذوب بالاتر با هیدروکربن وارد واکنش می شوند. به عنوان مثال، در آلیاژ Ni20Cr مقدار زیادی کاربید کروم پس از فرآوری ملاحظه شده است. این تکنولوژی برای تولید تناژی پودر فولاد توسط Sumitomo و دیگران به کار گرفته شده است، اما به نظر میرسد چندان از لحاظ اقتصادی مقرون به صرفه نیست. از طرف دیگر، پودر آلومینیم تولید شده با استفاده از آسیا کاری تحت اتمسفر هیدروکربن، به میزان زیادی به شکل پولک برای رنگدانه ها و پوشش ها به کار برده می شود. به این ترتیب، اگر آسیا کاری در اتمسفر هیدروکربن با روش اتمیزاسیون با سیال هیدروکربن از نظر محصول تولیدی قابل رقابت باشد، ممکن است هزینه خشک کردن و سیستم های بازیابی حلال در روش آسیاکاری به طور کامل حذف شود و جابجایی محصولات نیز به شکل ساده تری صورت پذیرد.
روش های دو سیاله (۲ ): اتمیزاسیون با سیال برودتی
با توجه به بحث هیدروکربن که در بالا مطرح شد، این تصور محتمل است که از یک گاز خنثی مایع برای اتمیزاسیون استفاده شود تا میزان جذب اکسیژن به حداقل رسیده و جذب کربن نیز حذف گردد. اگرچه گازهای مایع در مقایسه با آب(یا روغن) خیلی چگال نیستند و انرژی کمتری به مذاب منتقل می نمایند. از طرفی گازهای مایع همیشه در دمای جوش خود یا بالاتر از آن به کار می روند، در صورتی که در اتمیزاسیون آبی به واسطه دلایل عملیاتی، از جوشش زیاد آب جلوگیری به عمل می آید. همچنین، توان کوئنچ گازهای مایع به واسطه اثری موسوم به Leidenfrost به نسبت ضعیف است.
محققین آزمایشاتی را با نیتروژن مایع و آرگون در فشار چند صد بار انجام داده اند اما، نتایج چندان امیدوار کننده نبوده و هزینههای فرآیند بالا بوده است. به عنوان نمونه، نتایج در شکل ۱۲ نشان می دهد که نسبت های بزرگ گاز/ فلز بین ۱۵ – ۵ برای اتمایزینگ مس با گاز مایع استفاده شده در حالیکه، در اتمیزاسیون گازی متداول نسبت GMR تنها بین ۵ – ۲ قرار می گیرد.
اتمیزاسیون تک سیاله فشاری
فرآیندی که در آن مایع تحت فشار از میان یک نازل عبور می کند، قطعا یک روش متداول برای شکل گیری اسپری قطرات برای سیال هایی مانند آب، بنزین و غیره است. در واقع، این مهم برای فلزات مذاب نیز قابل انجام می باشد اما، مهمترین چالش آن چگونگی قرارگیری مذاب تحت فشار و یافتن یک نازل با مقاومت بالا در برابر سایش ایجاد شده توسط مذاب است که تحت فشار دارای سرعت بالایی خواهد بود.
شکل ۱۲ : چپ نتایج اتمیزاسیون با گاز مایع و راست نتایج اتمیزاسیون گازی
آزمایشاتی توسط Sheikhaliev روی گسترهای از آلیاژهای دمای پایین انجام شده و با انجام کارهای تکمیلی بر نتایج اولیه، تجهیزات بزرگی برای اتمایزینگ سرب با ظرفیت تقریبی t/h 2 به این روش ساخته شده است (شکل ۱۳ ). برای این فلز، استفاده از پمپ سانتریفیوژ برای قرار دادن مذاب تحت فشار مناسب است و نازل فولادی نیز عمر کاری خوبی دارد. این دستگاه بالغ بر ۲۰ سال به طور مناسبی با حداقل هزینه کار کرده و شات های پودری با اندازه mm 3 / 1 – 5 / 0 تولید نموده است. فرآیند به طور کامل اتوماتیک بوده و امکان آنالیز آنلاین شرایط تولید وجود دارد. یک مزیت مهم استفاده از نازل با جت چرخشی آن است که انحراف استاندارد محصول تقریب ا مشابه با پودرهای اتمیزه شده با روش گریز از مرکز و در حدود ۵ / ۱ – ۴ / ۱ می باشد (شکل ۱۴ ). این بدان معناست که بازده فرآیند در تولید محدوده اندازه باریک پودر بسیار عالی بوده هر چند که، ابعاد دستگاه اتمیزه بزرگ (با قطر تقریبی ۱۰ متر) است و به صورت باز عمل می کند.
از طرفی، سرب یکی از معدود فلزاتی است که به آسانی در هوای آزاد خنک می شود. این مطلب نیز درست است که ساخت پودرهای ریزتر نیاز به اعمال فشارهای بالاتر و نازل های کوچکتر دارد و این موضوع، منجر به افزایش چالشها در بحث سایش یا گرفتگی نازل می گردد.
جمع بندی
در طی مقالات تشریح شده در چهار بخش، نویسندگان تلاش نمودند که مرور جامعی بر روش های اتمیزاسیون در تولید پودر فلزات با تاکید بر اقدامات فعلی و پتانسیلهای موجود در آینده داشته باشند. روش های اصلی شامل اتمیزاسیون مذاب با گاز و آب هستند که به ویژه برای آلیاژهای با نقطه ذوب بالاتر به کار می روند. در حالیکه فلزات غیر آهنی مانند Pb ، Sn ، Zn ، Al ،… در برخی موارد با محدوده گسترده تری از روش ها شامل اتمیزاسیون
التراسونیک و گریز از مرکز قابل فرآوری هستند.
شکل ۱۳ : اتمایزر تک سیاله با جت فشاری- چرخشی برای تولید پودر سرب با ظرفیت ۲t/h
شکل ۱۴ : نازل با جت چرخشی در حال پاشش آب
شاخص های مورد نیاز برای مشخصه یابی پودر بسیار گسترده بوده و مواردی مانند شکل، اندازه، ترکیب (شامل سطح و توده پودر)، سیلان، چگالی حجمی، خواص مغناطیسی و ریزساختاری، رنگ، واکنش پذیری و فعالیت حین تفجوشی را شامل می شوند. با در نظرگیری گستردگی شاخص ها، انتخاب فرآیند اتمایزینگ و نیز عملیات نهایی پس از آن، شامل کنترل اندازه پودر از طریق غربالگری و تفکیک و عملیات حرارتی مانند احیاء یا آنیل،
بسیار مهم بوده و نقش اساسی در خواص پودر محصول دارد. این مقاله در مجموع حاصل تجربیات چندین ساله تیم نویسندگان آن در اجرای سایت های مختلف تولید پودر و تحقیقات گسترده روی مواد و فرآیندها طی سال های اخیر بوده است که در نهایت می تواند خلاصه ای از اتفاقات این صنعت و زمینه های پیش روی آن باشد و لازم است که بازار این صنعت بزرگ در سال های آتی، با جزئیات بیشتری مورد بررسی و تحلیل قرار گیرد.
مرجع
Joseph Tunick Strauss, PhD and John J Dunkley, PhD, The article of “How to make metal powders, part4: Centrifugal and other special atomization methods” published in Journal of Powder Metallurgy Review Magazine, Autumn 2022, pages 71-78